Indexable Insert Peripheral Grinding Machine
The W500GT peripheral grinding machine deeply integrates the concept of precision grinding with independent innovative technologies. With five - axis simultaneous control as the core, it creates a high - precision, high - efficiency, and highly flexible tool grinding solution. Through multi - axis collaborative motion, intelligent program optimization, and a full - process quality control system, it meets the stringent requirements for complex tools in fields such as aerospace, automotive manufacturing, and precision mold making.
It is suitable for the processing of various types of multi - profile indexable inserts. Its excellent grinding performance is widely used in the grinding and processing of carbide inserts, ceramic inserts, PCD inserts, and CBN inserts.
Main Configurations: |
Bosch Rexroth numerical control system |
The independently developed grinding software is suitable for the grinding of most inserts and non-standard grinding. |
Mechanical spindle |
Bosch Rexroth high-quality linear motors and torque motors |
Fagor high-quality optical grating ruler |
Sony high-precision online measurement and sensing system |
Schneeberger high-quality linear guide rails |
Automatic online measurement, automatic compensation, and regrinding according to the measurement results. |
Six-axis automatic loading and unloading robot |
Continuous display function of grinding precision |
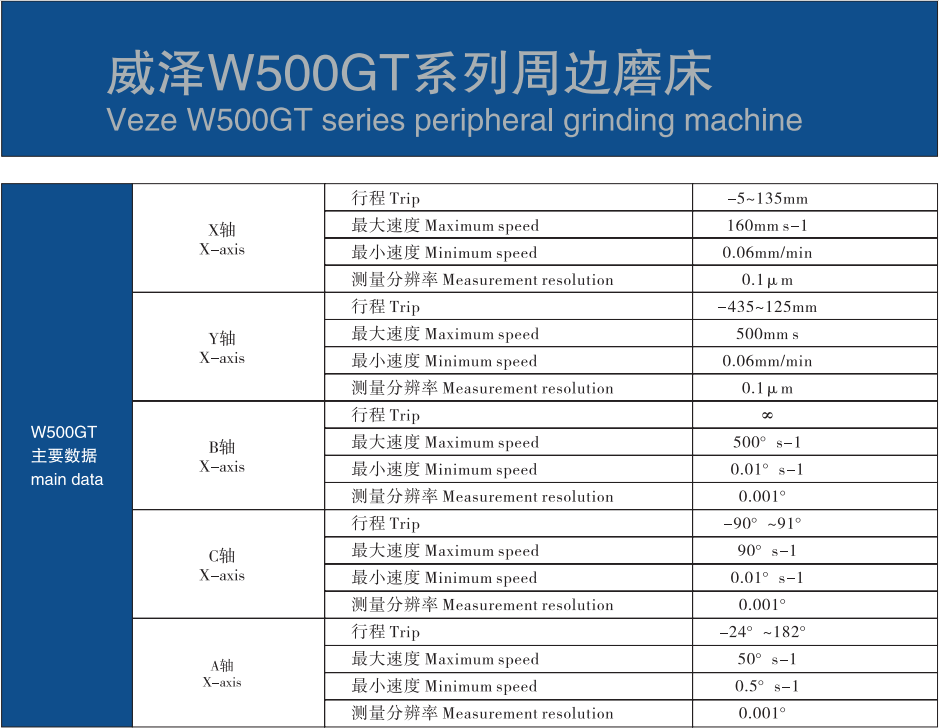
The W500GT adopts a five-axis simultaneous control system, supporting the linear motion of the X/Y axes and the simultaneous rotation of the B/C/A axes. It can perform multi-angle synchronous grinding on the complex curved surfaces and asymmetric cutting edges of tools. It is especially suitable for the processing of components such as aero-engine blades and inserts for irregular-shaped molds, which enables higher machining accuracy.
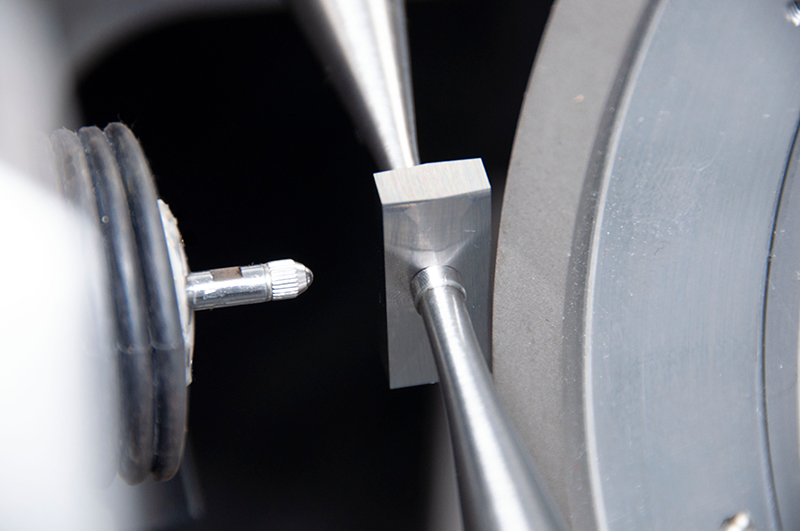
It is equipped with the graphical programming software independently developed by Weize, which supports the simulation of the grinding path to reduce manual programming errors. It comes with an OEE (Overall Equipment Effectiveness) function and supports free upgrades. There are various programming methods available, and it can be connected to external storage for online processing. The built-in force monitoring system can monitor the grinding pressure in real time, dynamically adjust the grinding parameters, and avoid problems such as overcutting or undercutting.
It is equipped with an Internet interface to accurately collect grinding data, enabling cloud storage and remote diagnosis. By integrating predictive maintenance algorithms, it can identify potential failures in advance, significantly reducing the risk of downtime. It provides a complete smart factory solution, and with comprehensive software and data interface services, it helps factories with their intelligent upgrading.
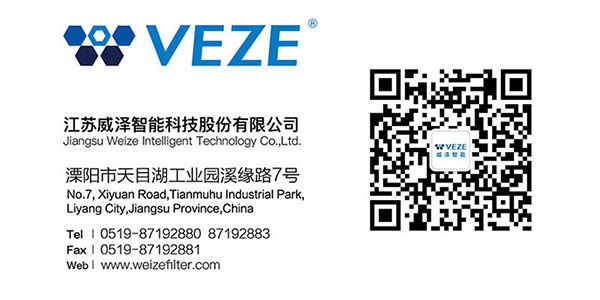